Sustainable Design Awards Toolkit
Section 2.5 Disassembling and Analysing Products
Find a broken/unused product from your home or buy one from a charity shop. Try to disassemble the product into its individual components. Electrical parts such as plugs and motors do not have to be disassembled. These components would be designed by engineers and are likely to be supplied as off the shelf parts. Make notes as to how the product was disassembled, how difficult and time consuming it was and if possible take pictures. Number and name each component, filling in the table found at the end of this section may help. Some material and processes identification help and common problems to look out for in the exercise are included next.
Identifying polymers
Polymer codes
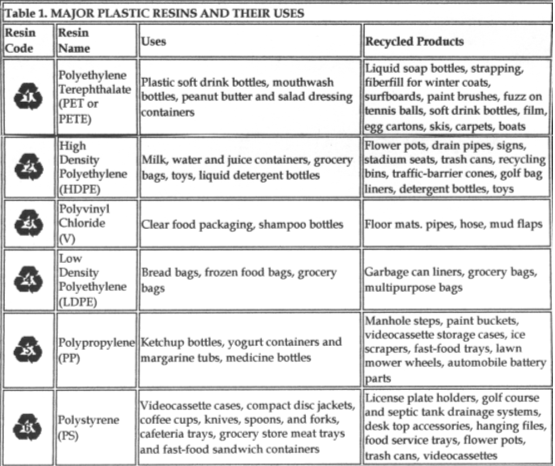
Source: www.plastics.ca/StaticContent/StaticPages?teachers/pdf/background.pdf
Some polymer characteristics
Plastic |
Density compared to water |
Characteristics |
Applicactions (if not included in above table) |
PET |
Sinks |
� |
� |
HDPE |
Floats |
Fairly stiff, strong resistant to chemical attack |
� |
LDPE |
Floats |
Weaker, softer and more flexible than HDPE |
� |
PP |
Floats |
Tougher and more rigid than HDPE. Very low density. High impact strength. Used for 'live' plastic hinges as can be flexed thousands of times with out breaking. |
� |
PS |
Sinks |
Solid - very brittle. Metallic ring sound when dropped
Expanded - soft and spongy
|
Medicine spoon
EPS disposable cups
|
Acrylic |
� |
Can have glass-like transparency. Very brittle - easily scratched/cracked |
Watch 'glass'
Car light units |
Nylon |
� |
'solid' nylon used for it's low frictional properties - usually creamy white colour. Can also be used as a fibre. |
Fast moving parts such as gears or bearings. Fibre form: toothbruch bristles |
PVC |
Sinks |
Stiff hard wearing
Add plasticiser - more flexible and rubbery
|
Drain pipes
Cables will be coated with flexible PVC 'leathercloth' car seats |
Common processing routes for plastics
Extruded - 'long' products such as drain pipes and curtain rails. Molten plastic is forced through a die, which contains a hole whose shape corresponds to that of the required article. The extrusion will then be cut into lengths. The cross section will be the same along the length. Used with plastics such as polythene, PVC and nylon and also metals.
Source: James Garratt 'Design and Technology' Cambridge 1994
Extrusion blow moulding
- bottles and hollow toys. Air is blown into a section of extruded plastic tube (parison) causing it to expand and take up the shape of the mould. Should have split line on both sides along length where the two sides of the mould came together. Will be one mark at centre of bottom where the parison (plastic extrusion) fed into the mould is cut off. PVC, polythene and polypropylene are common blow-moulding materials.
Source: James Garratt 'Design and Technology' Cambridge 1994
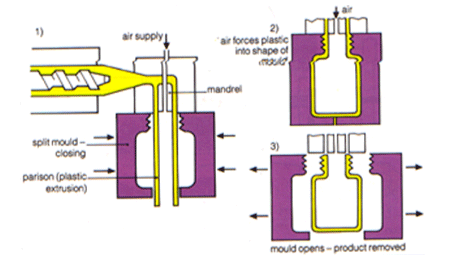
Injection moulding - cases for electrical appliances, toys and games, products for the car industry, kitchenware such as bowls and containers, often relatively complex forms. Molten plastic is forced into a mould. The mould consists of two or more parts that fit together, forming a cavity of the required shape. Should have one rough 'gate' mark where the polymer is injected into the mould. There may be several smooth circular marks caused by ejector pins pushing the component out of the mould. Polythene, polystyrene, polypropylene and nylon are typical injection moulding materials. Source: James Garratt 'Design and Technology' Cambridge 1994
Compression Moulding - electrical fittings such as plugs and sockets, saucepan and cutlery handles, bottle tops and toilet seats. A measured quantity of polymer is squeezed into shape between heated moulds. The mouldings have a high quality finish requiring only the removal of 'flash.' Compression moulding is usually used for thermosetting plastics such as phenol, urea and melamine formaldehyde. Source: James Garratt 'Design and Technology' Cambridge 1994
Vacuum Forming - chocolate box liners, egg boxes, seed trays, shop signs and fittings, some motor car dashboards, wash basins and baths. Mainly for shallow components made from thin sheet. A sheet of polymer is heated until soft and rubbery. The air is then evacuated from beneath the sheet. This allows the normal 'outside' air pressure to push down on the softened sheet, forcing it to take up the shape of the mould. Acrylic, polystyrene and PVC are typical vacuum forming materials.
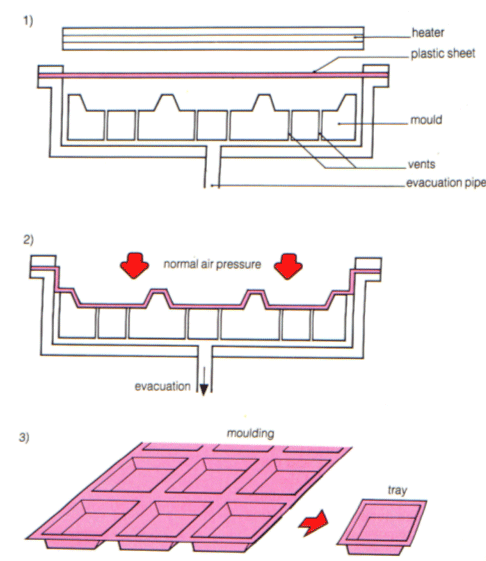
Source: James Garratt 'Design and Technology' Cambridge 1994
Rotational Moulding -
Rotational moulding is a method for manufacturing hollow plastic products. It is best known for the manufacture of tanks, but designers all over the world are starting to realise that it can be used to make many different types of plastic parts. Some of the sectors that it services include medical products, consumer products, agricultural and garden equipment, automotive and transportation components, toys, leisure craft and sporting equipment, furniture, materials handling articles and highly aesthetic point-of-sale products.
An overview of rotational moulding:
A hollow mould is filled with a powder resin and then rotated bi-axially in an oven until the resin coats the inside of the mould and cures. The mould is then cooled and the part removed. (Source: http://www.rotationmag.com/article3.htm)
Calendaring - process used to produce plastic bags.
Expanded Polystyrene Production - Polystyrene beads are expanded to about 40 times their original size using pentane as a blowing agent. They are then heated with steam inside a mould. The final expansion takes place and the beads coalesce to give a shaped moulding.
(For information concerning manufacturing, fabrication and finishing processes for other materials, please refer to pp 264-333
Eddie Norman, Jay Cubitt, Syd Urry, Mike Whittaker, Advanced Design and Technology, Third Edition, Longman, 2000)
Potential eco-design problems to look out for and some possible design solutions
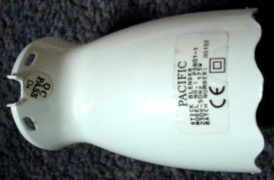 |
If sticky labels are not removed they can contaminate the resulting polymer
Could use indented lettering
|
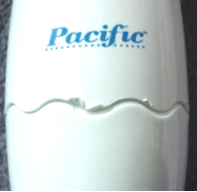 |
ABS
PP
|
Two different materials are used for the main casing. When disassembled the two parts would have to be separated and recycled individually.
If possible use the same type of polymer throughout the design
|
|
Have snap fits been used?
Snap fits can mean a reduction of material usage as screws and glues are not required. Snap fits are easy to assemble as they simply push together. They do not require special tools for disassembly. They can hinder disassembly, however if they are difficult to push back out of place.
Force required to disassemble snap fits can be changed using design, namely the material thickness used. Alternately could be easier to screw together or use active disassembly methods
|
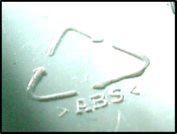 |
Have all components been labelled with their material type?
These are usually found as indents, often found inside the casing. Without these labels
people will not know how to recycle the components.
Indent recycling aids into all components
|
Double or 2-shot or co-injection moulding combines two plastic materials by injecting them separately into the mould to form a single part with two visible colours. Co-injection moulding is only possible with polymers that have good adhesion properties. This implies compatibility for recycling. Environmental problems occur, as the two materials co-injected are often different polymers that cannot be recycled together.
|
This toothbrush has been co-injection moulded. Two different materials that cannot be recycled together are now permanently bonded, making disassembly near impossible.
Different coloured components could slot together. Use different colours of the same material?
|
# |
Component name |
Material |
Surface finish |
Processing route |
Method of Disassembly |
ex.1 |
Bottom casing |
ABS |
Green pigmentation |
Injection moulded |
Snap fits to top casing - levered apart with screwdriver |
ex.2 |
Packaging |
Expanded polystyrene |
N/a |
Expanded and injection moulded |
N/a |
ex.3 |
Packaging |
Cardboard |
Colour Screen Printing |
Stamped out of sheet. Folded and glued together with hot glue gun |
N/a |
ex.4 |
Cable grip |
Copper |
N/a |
Stamped out of sheet |
Screwdriver used to unscrew 2 screws from top casing |
|